Donnerstag, 24. Oktober 2024
Überblick
Ein OEM (Original Equipment Manufacturer), der Millionen Stück eines elektronischen Konsumproduktes produziert, arbeitet mit zwei verschiedenen Outsourcing-Partnern zusammen, um kleine Chip Scale Package (CSP) von integrierten Schaltungen (IC) mit den Abmessungen 2mm x 3mm zu programmieren. Beim Pre-Programming werden ICs vor dem Einsatz in die Baugruppe programmiert und anschließend in der Line verbaut. CSP-Bausteine bieten OEMs eine kompakte und leichte Bauform, die ideal für moderne Konsumgüter sind. Aufgrund ihrer geringen Größe und empfindlichen Eigenschaften erfordern CSP-Bausteine eine zuverlässige und präzise Handhabung während des gesamten Fertigungsprozesses, um Beschädigungen zu vermeiden.
Nach der Endmontage stellte der OEM fest, dass die Produkte in der Praxis eine hohe Ausfallrate aufwiesen. Eine Untersuchung ergab, dass die Ursache der Ausfälle auf eine unsachgemäße Handhabung der CSP-ICs während des Programmierprozesses zurückzuführen war und die Bausteine dadurch beschädigt wurden. Diese Fallstudie analysiert die Ursache der beschädigten CSP-Bausteine, diskutiert die Kosten der Qualität und zeigt, wie der Kunde die Ausfallraten im Feld durch die Standardisierung der Programmierprozesse signifikant reduzierte.
Die Fallstudie
Aufgrund einer signifikanten Nachfragesteigerung für ein Endverbraucherprodukt teilte der OEM den Programmierprozess für den 2mm x 3mm CSP-ICs auf zwei Outsourcing-Partner auf. Jeder der Outsourcing-Partner verwendete einen anderen Anbieter für automatisierte Programmierungssysteme. Partner #1 verwendete ein PSV-System zur automatisierten Bausteinprogrammierung. Partner #2 nutzte ein kostengünstigeres automatisierten Programmiersystem, das für seine schnelle Handhabung bekannt ist.
Nachdem die CSP-Bausteine von den Outsourcing-Partnern programmiert worden waren, wurden sie zu einem EMS-Partner (Electronic Manufacturing Services) geschickt, der die Endmontage durchführte. Nach der Markteinführung stellte der OEM eine hohe Ausfallrate seines elektronischen Konsumproduktes fest. Der EMS-Partner führte eine gründliche Fehlerursachenanalyse durch. Hier zeigte sich, dass das Produkt ausfiel wurde, wenn es über längere Zeit bei hohen Temperaturen im Einsatz war. Die Fehler konnten auf beschädigte CSP-Bausteine zurückgeführt werden, die an den Ecken oder Kanten Risse aufwiesen (siehe Abbildung). Eine weitere Analyse der programmierten Bausteine der beiden Outsourcing-Partnern zeigte, dass die meisten defekten Bausteine von Partner #2 stammten.
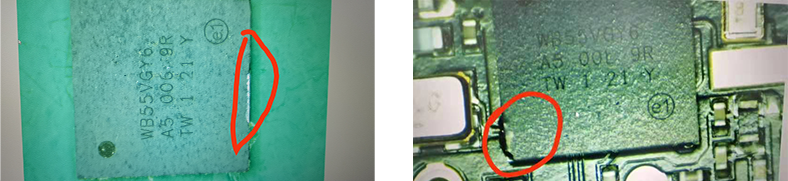
Was kostet Qualität?
Qualität und Zuverlässigkeit wirken sich direkt auf die Gesamtkosten der Programmierung aus. Systeme mit hohen Programmiererträgen reduzieren Nacharbeitskosten und verbessern die Produktionseffizienz. Dies wird umso wichtiger, wenn es um die Programmierung kleiner Bausteine wie CSP, WLCSP oder bedrahteter Gehäuse geht. Schnelligkeit und niedrige Programmierkosten können einen hohen Qualitätsstandard nicht ersetzen. Die Kosten des beschriebenen Fertigungsfehlers wirkten sich auf die gesamte Lieferkette aus. Denn hier wurde jedes Unternehmen, dass an der Entwicklung, Produktion und dem Verkauf des Endprodukts beteiligt war durch verpasste Termine, Kostenüberschreitungen, Überstunden, Nacharbeit und Kundenbeschwerden beeinträchtigt.
Die Berechnung der Fehlerkosten wird exemplarisch mithilfe der 1-10-100-Regel deutlich. Die erstmals von George H. Labovitz und Y.S. Chang im Artikel „Quality Costs: The Good, The Bad and The Ugly“ beschriebene Regel besagt, dass jeder Dollar, der in die Fehlervermeidung investiert wird, 10 Dollar kosten würde, um den Fehler zu einem späteren Zeitpunkt zu beheben und 100 Dollar, wenn der Fehler gar nicht behoben wird. Ziel der 1-10-100-Regel ist es, den exponentiellen Anstieg der finanziellen Kosten aufzuzeigen, der davon abhängt, wann Fehler aus dem Entscheidungs- oder Produktionsprozess entfernt werden. Die Sicherstellung der Qualität bereits in den frühen Phasen des Fertigungsprozesses ist für OEMs von entscheidender Bedeutung.
Fehleranalyse
Das Ergebnis der OEM-Fehleranalyse, bei der eine Million Bausteine auf dem automatisierten Programmierungssystem von Data I/O programmiert wurden, ergab eine Fehlerquote von 0,01% und einen dreimal höheren Programmierdurchsatz als die alternative Lösung lieferte. Der Unterschied war so signifikant, dass der Outsourcing-Partner #2 von dem Projekt ausgeschlossen wurde und das Programmierverfahren mit den Systemen von Data I/O standardisiert wurde, um die erforderliche Qualität sicherzustellen.
Programmiervorteile für CSP-ICs
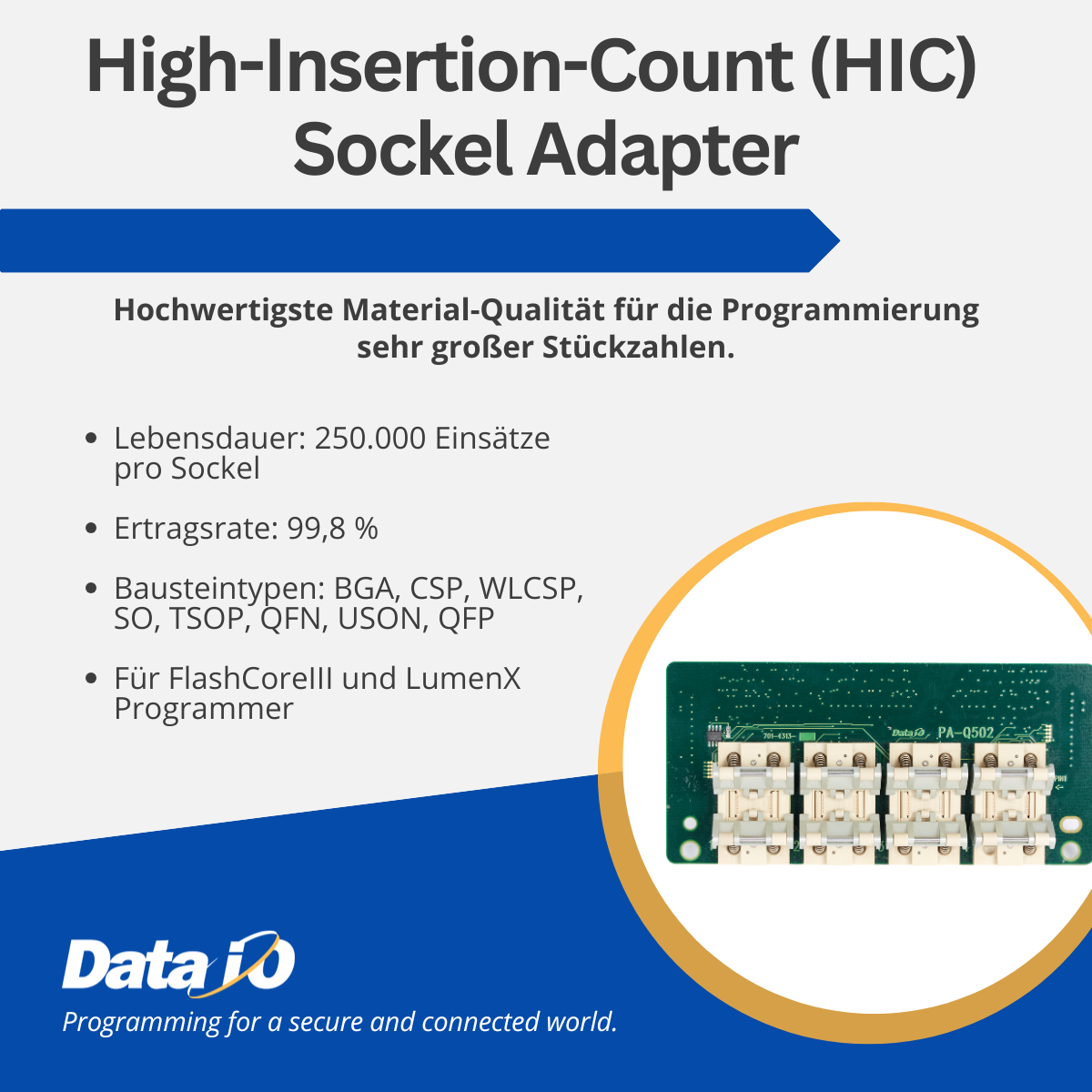
Für eine noch genauere Handhabung des Programmierauftrags der 2mm x 3mm CSP-ICs wurde bei Outsourcing-Partner #1 entschieden, High-Insertion-Count (HIC) Sockeladapter von Data I/O Programmierung einzusetzen. HIC-Adapter wurden für die Massenproduktion entwickelt, um die Produktionsauslastung zu maximieren. Jeder Sockel ist für 250.000 Kontaktierungen ausgelegt und bietet eine Zuverlässigkeit von mindestens 99,8% oder höher. Zudem sind HIC-Sockel die bewährteste Lösungen zum Schutz und zur Programmierung sehr kleiner Gehäusetypen. Denn die Programmierkontakte bestehen aus sehr hochwertigen Materialien, die rauscharme Programmiersignale für eine saubere Signalintegrität an die Bausteinkontakte liefern. Darüber hinaus sorgen federnde, vergoldete Edelstahlstifte für eine genaue Wiederholbarkeit und lange Lebensdauer der einzelnen Sockelkontakte. Die Programmierbausteine werden mit einer präzisen Pick-and-Place-Technologie in den Sockeladapter gelegt und nach der Programmierung in das Outputmedium weiter transportiert.
